This Page is HomeUpdates
What's New
Penta-Ocean Construction Co., Ltd.
Automated welding of waterproof sheets in mountain tunnel construction
Tokyo, Japan - February 6, 2023 -Penta-Ocean Construction (President: Takuzo Shimizu) and Daiei Kouki Co., Ltd. (President: Masahiko Kobayashi) have jointly developed the "Automated Waterproof Sheet Welding System," which automatically installs waterproof membranes on the surfaces of mountain tunnels. Through the verification tests performed at the site of “Sasebo Road Yumihari Tunnel Construction Project (Client: West Nippon Expressway Co., Ltd. Kyushu Branch)” for a 24m-long waterproofing work, we confirmed that the system helps achieve labor saving and improvement of construction safety.
Conventionally, the process of waterproof sheet installation in mountain tunnels involved the manual operation by three workers where they would perform hand-welding by passing a welding machine to each other in a circumferential direction of the tunnel (Figure 1). Hand-to-hand delivery of the machine and operating it manually in a narrow space at high elevations on the rolling scaffold platform was one of the most back-breaking tasks. The sheet-welding required handiwork of skilled workers, as the waterproof membrane needed to be pulled downward in parts to fit the uneven surface of the underlining shotcrete.
The new system allows for unmanned welding of the waterproof sheets, by operating an autonomous welding machine on the guiding rail attached to the rolling scaffold platform (Figure 2). The movement of the autonomous welder is actuated by the seesaw-like part, the slide, the rotator and the balancers. The welder effectuates automated installation of sheets, as it balance-walks in all 3D directions along the sagging and irregular welding line (Figure 3). Furthermore, by controlling the welder’s travelling speed at a constant rate in accordance with its welding speed, we achieved a high construction quality of the welded area. Also, the sheet fixation jig at the top of the welding roller helps smooth out creases of the sheet before it is fed into the welding roller.
During the verification tests at the site, one worker served as an operation supervisor and confirmed the successful performance of the automated welding along the entire length of the welding line, reducing manual operation of skilled workers up on the high scaffolding and freeing them from laborious tasks. The time required for the operation using this new technique was equivalent to that of conventional manual welding, and visual check and pressure tests confirmed the high construction quality of the welded area.
Going forward, we will introduce this technology across various construction sites. By pursuing further expansion in the scopes of automated operation such as sheet stretching, quality control of welded area and improvement of welding speed, we will strive to enhance productivity and improve construction safety in the entire waterproofing work, which is an integral part in the construction cycle of mountain tunnel construction.
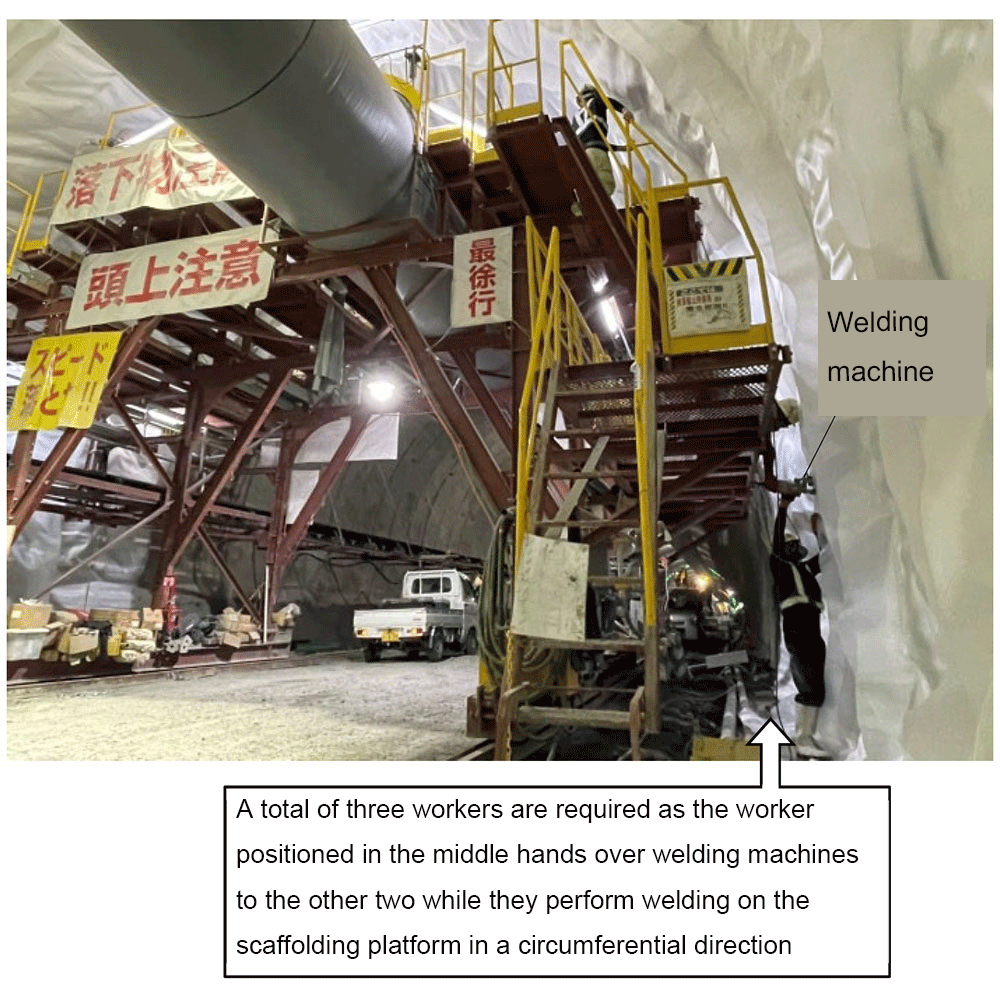
Fig.1 Conventional welding operation
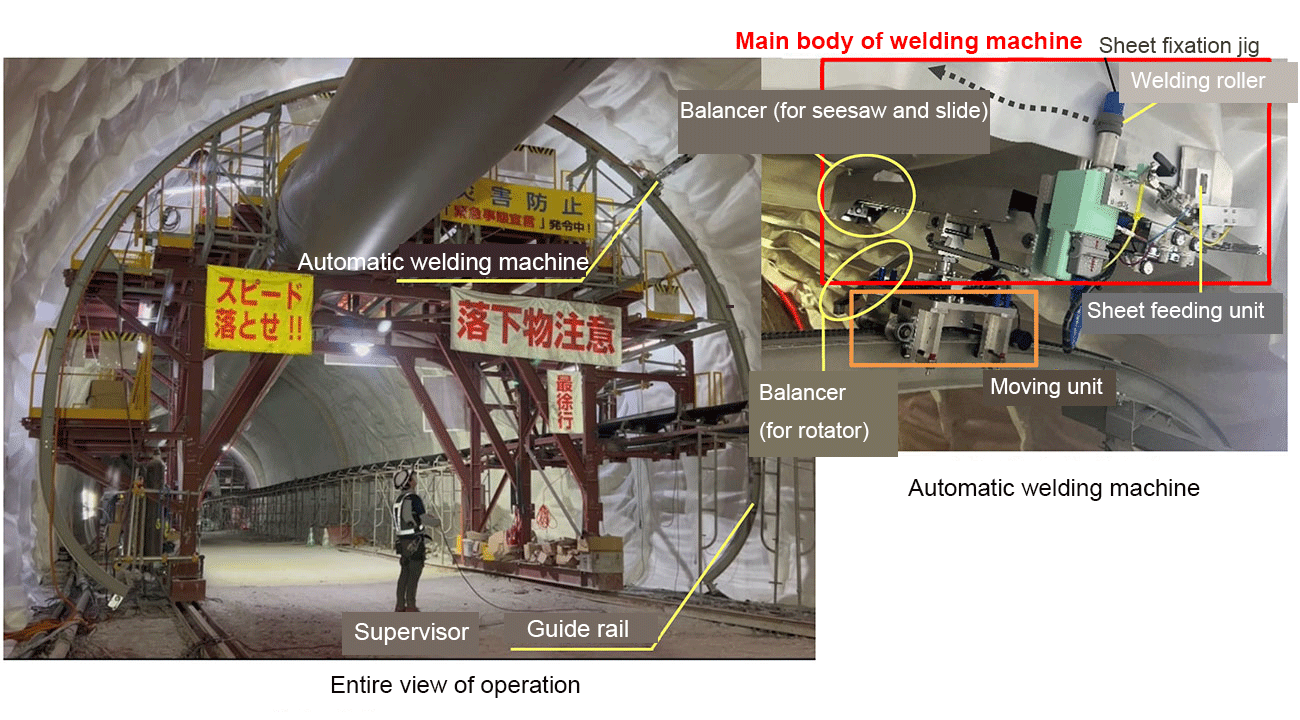
Fig.2 Waterproof sheet automatic welding system
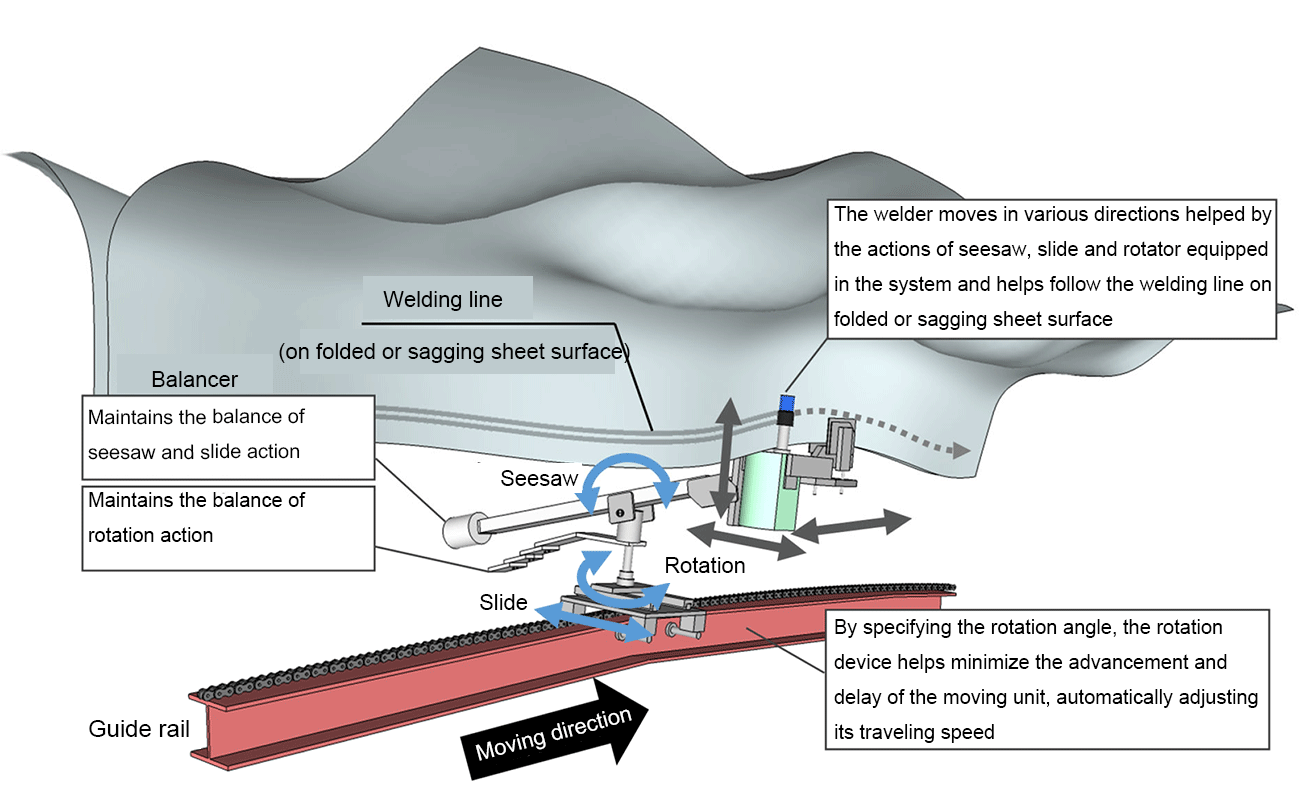
Fig.3 Image concept of welding operation by following the folded and sagging welding line