This Page is HomeUpdates
What's New
Penta-Ocean Construction Co., Ltd.
Takuzo Shimizu, President, CEO and Representative Director
Construction of “SEADOM-7”, an Underwater Rubble Levelling Robot
Tokyo, Japan - Sep. 12, 2022 - Penta-Ocean Construction has constructed a new rubble leveling robot "SEADOM-7" that can efficiently and highly accurately level rubble mounds for harbor construction. It is an eight-legged walking underwater work robot, which is less affected by waves and can be expected to operate at a high rate even in waters with severe marine conditions.
In an attempt to reduce manpower and improve the workability of rubble leveling by divers, we have built five rubble leveling robots so far since the first one was built in 1986, and have accumulated a lot of experience. The new model is equipped with a raking device and a compaction device using a weight, and enables automated construction through the use of ICT . In the past, the conventional rubble leveling method, in which weight is dropped using a crane barge, has been used in many projects, and this is the world’s first underwater robot equipped with a weight.
In order to create firm rubble mounds so that the gravity-type structures will not sink or tilt, the mound is precisely leveled with a raking device and compacted firmly with a weight (underwater weight 18.1 tons, bottom area 4 m2, maximum drop height 2 m), instead of the roller pressing method of the old robot. The weight used in the conventional method using a crane vessel has an underwater weight of 50 tons and a bottom area of 10m2, but its weight per unit area is almost the same as the weight of this robot.
The operator uses the underwater sonar to monitor the shape and height of the rubble mounds in real time, while the AI system determines the optimum weight dropping height and the number of times to improving construction accuracy and work efficiency.
The automated construction technology incorporates high-precision sensors and an automatic control system. The system imports from the BIM/CIM cloud the survey results after placing rubble, as well as the 3D design data of the rubble mound. It then calculates the differential amount of surface unevenness based on these data, and plans the following work procedure and executes. After the leveling work is completed, the 3D finished-shape data of the rubble mound measured by the ultrasonic sensors is sent to the BIM/CIM cloud for smooth data utilization, including real-time work progress management, leading to contribution in the overall productivity improvement of the project.
Features
a) Enables highly-accurate and firm compaction of mounds composed of rubble weighing 500 kg/piece or less
b) Improves construction accuracy and work efficiency by calculating the optimum weight dropping height using an AI system
c) Operates automatically by controlling hydraulic and electrical apparatus using sequence control
d) Improves productivity by linking data from the site to the BIM/CIM cloud and by effective use of 3D data
Construction work flow
(1) Moving and positioning: The robot is moved to the designated position and adjusted the direction according to the rubble leveling procedure.
(2) Surveying: Five ultrasonic sensors mounted on the rake cart measure the unevenness of the rubble mound.
(3) Rake leveling: The rake moves back and forth to level the rubble mound to the desired height.
(4) Weight compaction: Weight is dropped from the optimum height calculated by the AI system to firmly compact the rubble mound.
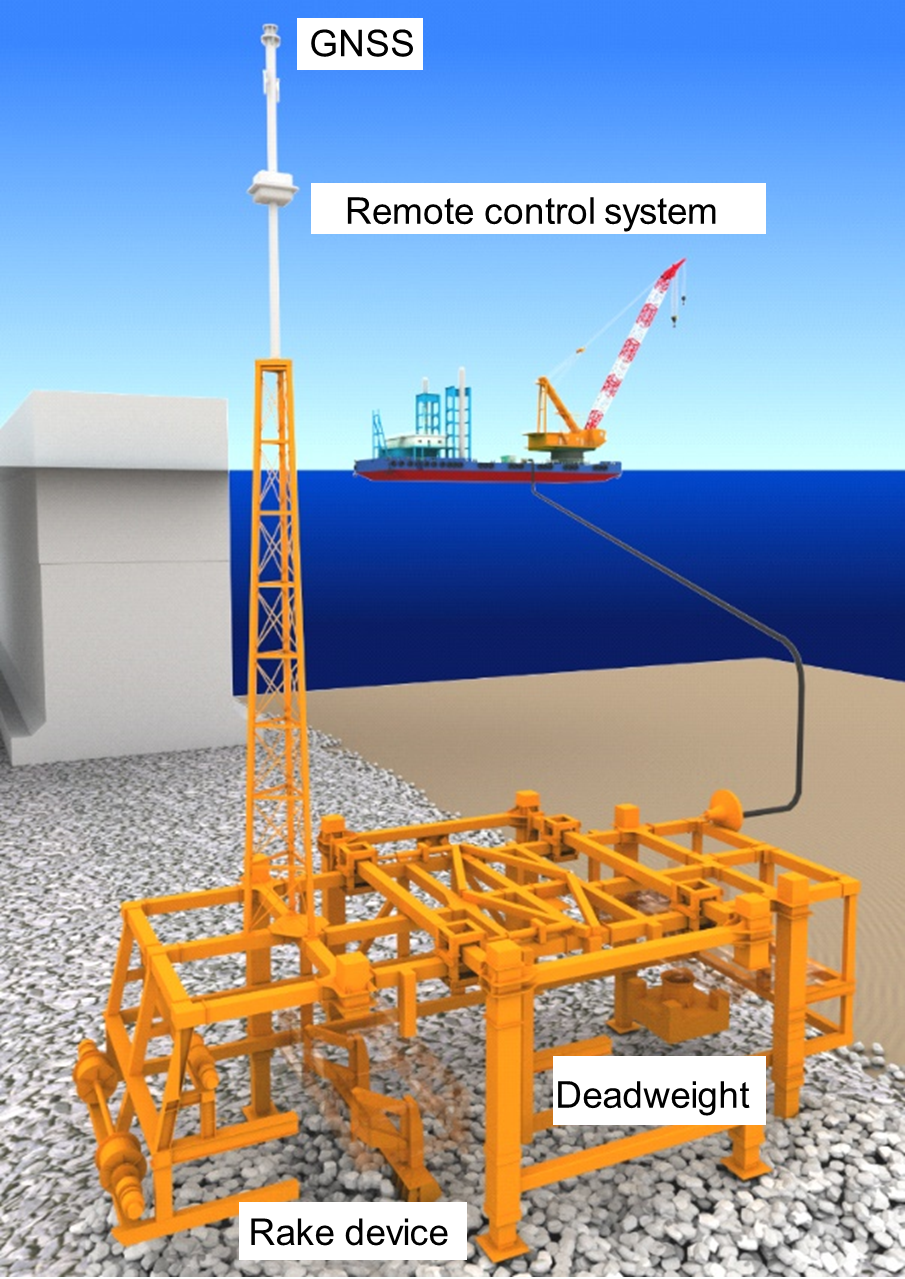
Conceptual image
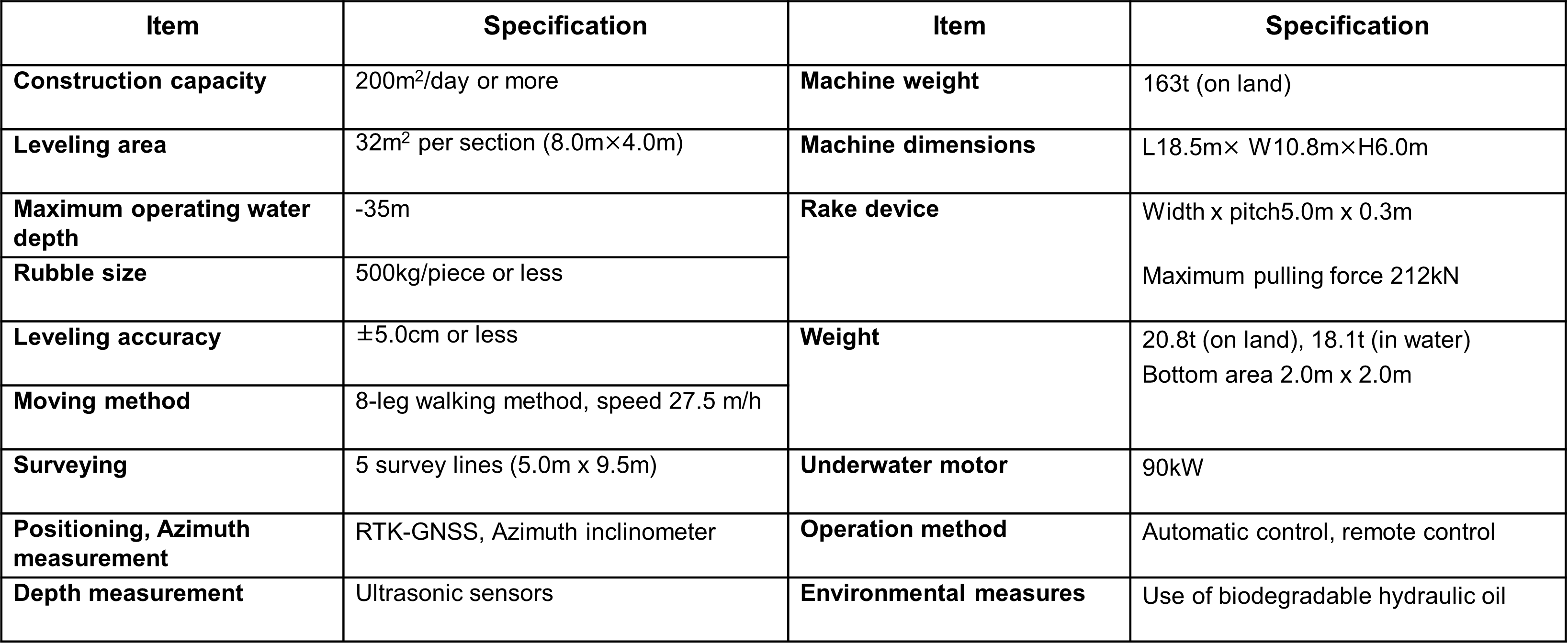
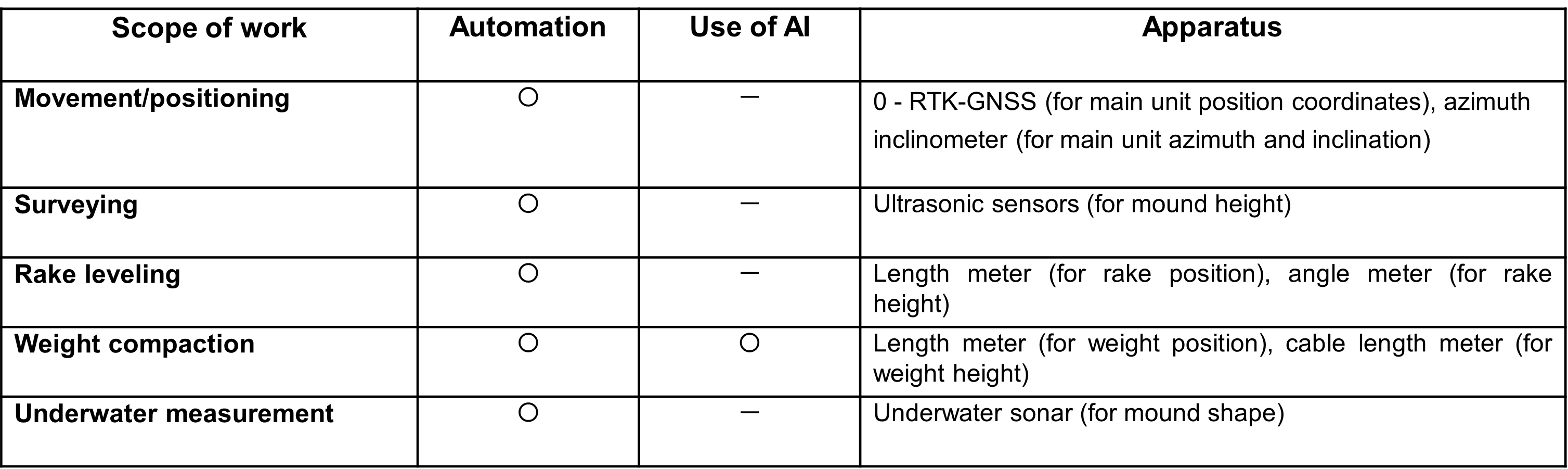