This Page is HomeUpdates
What's New
Penta-Ocean Construction Co., Ltd.
Porous Resin Sand (PRS) Received Performance Evaluation of Building Materials
Tokyo, Japan - September 1, 2022 -The fourteen companies participating in the PRS Method Study Group *1 (led by Asanuma Corporation, Chairman: Dr. Akio Matsui, from Asanuma Corporation, Technical Research Institute), which was established within the Crack Control Bar (CCB) Method Association*2, received the Performance Evaluation of Building Materials*3(No. 22-01) from the General Building Research Institute (GBRC) on May 16, 2022, for a joint filling method (hereinafter referred to as "Method") using porous resin sand (hereinafter referred to as “ PRS”, see Figure 1 and Table 1).
The Method was first developed in 2016 for filling joints of concrete frames for RC/SCR buildings, and it has since been used on fifteen actual projects (as of July 2022). We conducted verification tests on the performance of the PRS joint filler, in terms of (1) Concrete adhesion, (2) Sinking resistance on exposed joints, and (3) Crack dispersion, and demonstrated that the Method does not cause cracks at the adhesive interface between concrete and filler, nor does it induce cracks, creases, or surface voids on the finished surface. The Method went through an assessment by the third-party evaluation organization, and was granted the Performance Evaluation of Building Materials.
The ten companies intend to apply the Method to construct steel-framed buildings, etc., mainly in design-build projects, in order to achieve more sophisticated building design and construction.
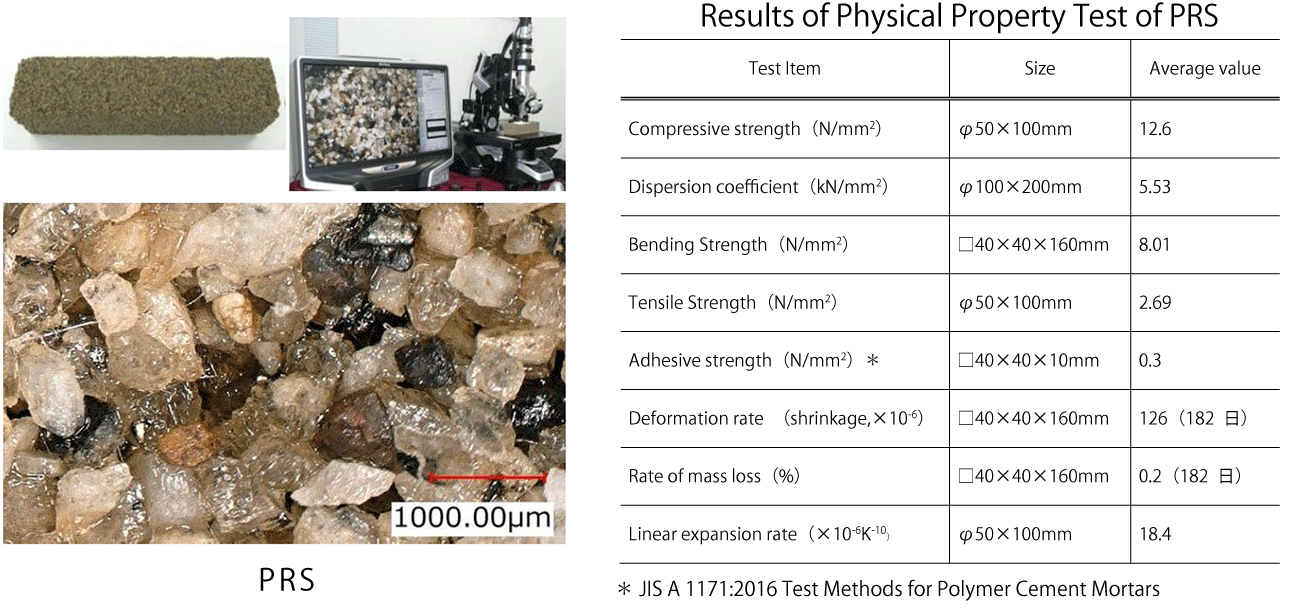
Figure 1 and Table 1:Results of Physical Property Test of PRS
■Performance Evaluation details
Performance Evaluation of Building Materials: Porous Resin Sand (PRS), GBRC Material Certification No. 22-01
Polar Resin Sand (PRS) used in the joint of concrete surface according to "Manual for Construction of Joint Filling Method Using Polar Resin Sand (PRS)" shown in the evaluation summary report, has the following performance.
(1) Adhesion to concrete:
The adhesion strength (direct tensile test) of PRS to concrete is more than 1 N/mm2.
(2) Sinking Resistance on exposed joints:
The depression deformation of the joint exposed PRS surface is less than 0.1 mm
(3) Crack dispersing abilities:
PRS has crack dispersion properties for joint width variation up to 0.4 mm.
■Development Background
Cracks and other flaws in the finishing layer of concrete walls prepared for wallpapering, etc. may cause aesthetic and durability problems. It is one of the events that all parties, including the end-users, designers and contractors, want to avoid. At the same time, when applying wallpapers or paint directly on walls that are provided with crack-inducing joints during the construction of concrete frames of RC and SRC buildings, conventional joint fillers have not been actively used, due to the higher possibility of eventual design flaws.
As a specific example, when we use mortar as joint filler, cracks are more likely to form at the adhesive interface between concrete and mortar, and these cracks may appear on the finished surface. On the other hand, when we apply sealing agent to joints for the sake of elasticity, the volume reduction may cause a progressive concavity from the surface of the frame, resulting in creases on the wallpaper surface, or a dent when pressed with a finger. Consequently, in order to avoid cracks, creases, and voids on the finished surface of the filled joints, it is necessary to use a sealing material with specific crack dispersion, compressive strength, and low volume loss in response to changes in the joint shape (Figure 2).
In the Method, we chose PRS as a joint filler. PRS is developed from a mixture of silica sand and fiber resin, which results in a porous structure that provides a certain degree of adhesion, resistance to collapsing, crack dispersion, and compressive strength.
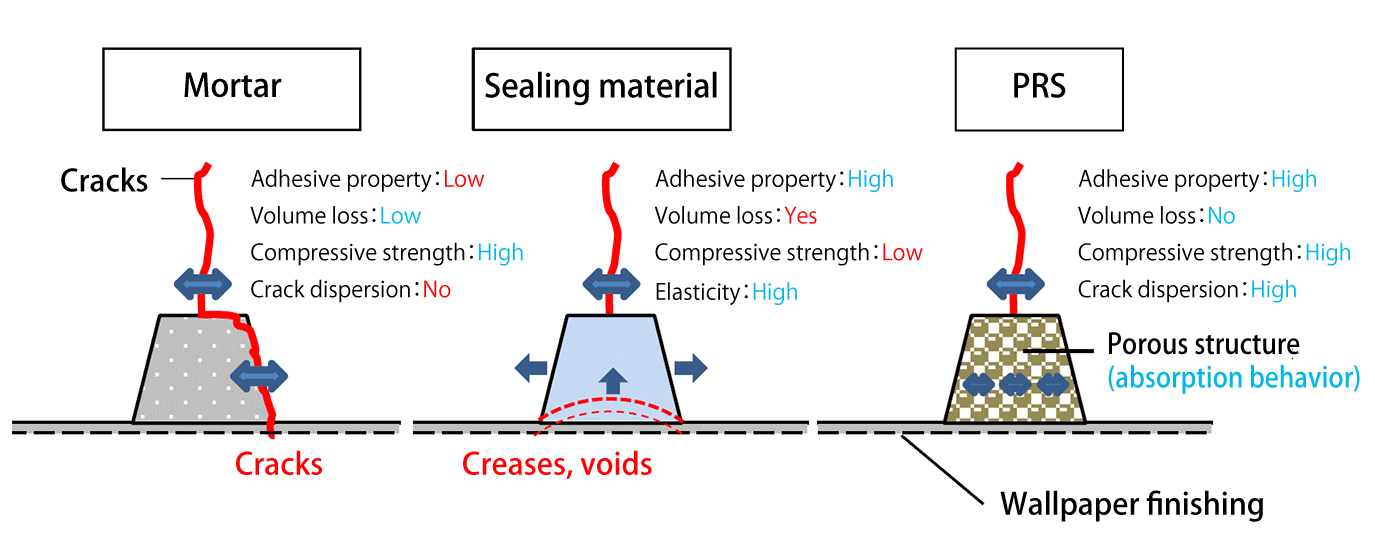
Figure 2: Performance comparison of joint filler (Joint cross section)
■PRS joint filling method
[Outline]
The Method is used to crack-induce joints in concrete frames of RC and SRC buildings. By filling the joints with PRS, which is made from a mixture of silica sand and fiber resin, PRS absorbs compressive and tensile strengths exerted on the inside of the PRS, according to the deformation of the joint shape, thereby preventing cracks in the directly-attached wallpaper surface.
The Method is applied to the joint of concrete structure or concrete members, and when the joints exposed to the wall or ceiling to which the interior restriction applied, the area of the joint facing the interior is limited to within 1/10 of the area of each surface (At least 1.2 m above the floor).
[Technology Features]
- 1. The crack dispersion property of the joint material reduces the width of a single crack and prevents the occurrence of cracks, creases, and voids on the directly-attached wallpapered surface (Photo 1).
- 2. Since all materials are prepacked, no material measuring is required during installation, and materials mixing is simple and accurate.
- 3. By using the CCB method, which induces shrinkage cracks in the joints (Photo 2), in combination with the Method, we can achieve more far-reaching prevention of deformation of the directly-attached wallpaper surface.
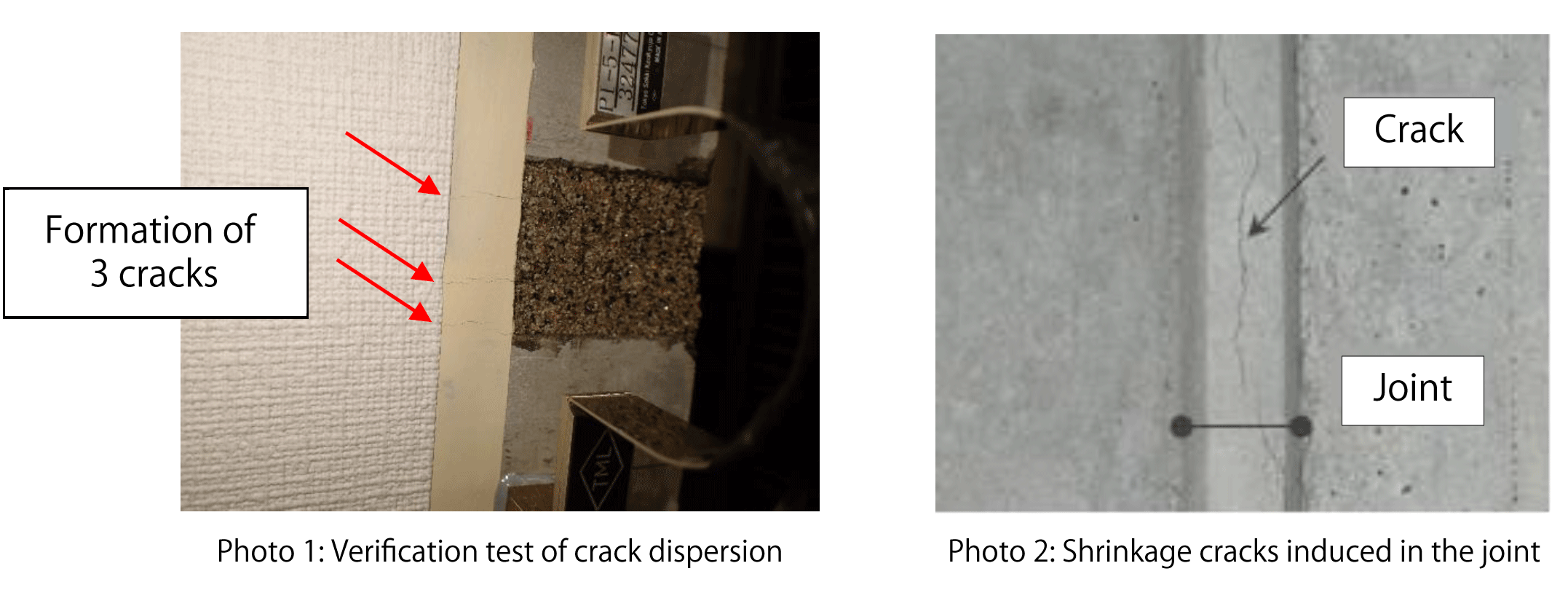
[Used materials (Photo 3)]
PRS resin: Epoxy resin [Main agent (with fiber): Hardener = 3:1]
Primer: Epoxy resin [Main agent: Hardener = 2:1]
Silica sand: Reverse sand No. 5 (Heated at 1,000°C)
Silica sand, primer and hardener are all pre-packed (made by AOI Thomas Co., Ltd.)
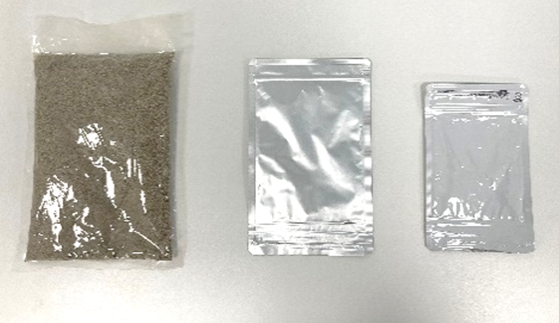
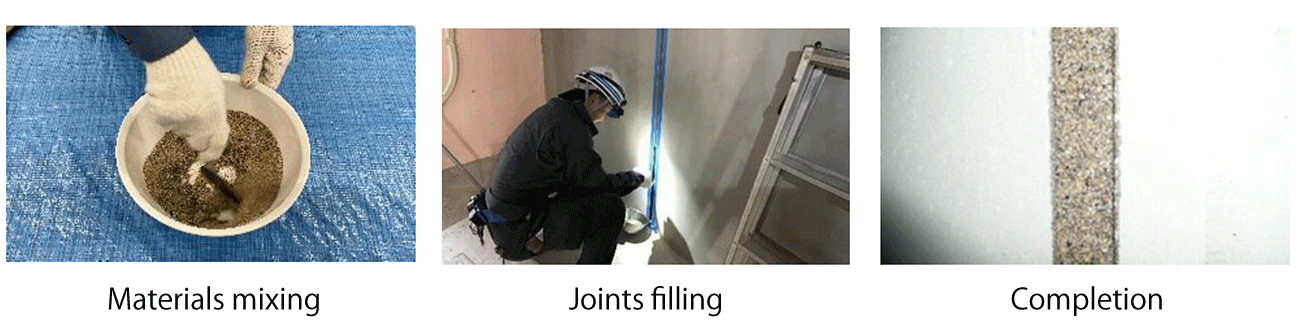
[Scope of users and design supervisors]
The CCB construction method can be used by joining the CCB Method Association as a supporting member.
[Scope of the contractors]
The scope of contractors is limited to those who have joined the CCB Method Association and who belong to the PRS Method Study Group. There are two types of membership: regular members and limited-term members.
[Related patents]
No.7025196 Joints and Filling Method for Buildings
■Future Development
The CCB Method Association shall require that construction sites using the PRS joint filling method be supervised by a CCB Method Construction Management Engineer who has been certified by the Association as having a comprehensive understanding of the Method. The CCB Construction Management Engineer certification is granted to those who have completed a training course conducted by the Association (which must be renewed every five years) and have been certified by a test as having the appropriate level of knowledge and skills.
The construction sites where the Method is used shall be supervised by a designated construction manager who fully understands the Method.
The acquisition of Performance Evaluation of Building Materials certification by a third-party assessment organization has increased the reliability of the said technology for preventing surface flaws of concrete frame joints by using PRS fillers, and further application of the PRS joint filling method to actual projects is expected.
Going forward, we will strive to promote the Method, including the training of construction management engineers.
- *1 PRS Method Study Group
As of July 2022, 14 regular member companies (representative company: Asanuma Corporation) are members of the CCB Construction Method Association’s study group.
[Member companies] Asanuma Corporation, Kumagai Corporation, Nishimatsu Construction, NIPPO Corporation, Tobishima Corporation, Dainippon Construction, Haseko Corporation, Tokyu Construction, Penta-Ocean Construction, Sumitomo Mitsui Construction, Kyoritsu Construction, Asunaro Aoki Construction, Matsui Kensetsu, Okumura Engineering Corporation - *2 The Crack Control Bar (CCB) Method Association
http://ccb-koho.com/ (Japanese only)
The Crack Control Bar (CCB) Method Association was founded on April 1, 2012 (as of July 2022, it has 17 regular member companies and 266 construction projects). It was established with the purpose of promoting the CCB construction method, improving its technology, and ensuring its sustainable development. - *3 Performance Evaluation of Building Materials
The General Building Research Institute (GBRC)/ Performance Evaluation of Building Materials
https://www.gbrc.or.jp/building_confirm/kentikuzairyo_shomei/